Interesting facts about
E-Coating
E-coat technology offers reliable corrosion protection, uniform coating thicknesses and high cost-effectiveness – an indispensable coating process in industrial surface technology.
What is e-coating?
E-coating, is an innovative further development of dip coating based on the electrochemical deposition of paint particles. In this process, workpieces are completely immersed in a conductive aqueous paint dispersion consisting of resins, pigments, additives and water.
By applying a DC voltage between the workpiece and the counter electrode, electrically charged paint particles migrate specifically to the surface of the workpiece and are deposited there.
Based on the principle of electrophoresis and electrocoagulation, a uniform, compact coating film is formed – even on hard-to-reach areas, edges, cavities or drill holes.
This property makes E-Coat particularly suitable for components with complex geometries, such as those often found in industry.
Two main types of e-coating
Depending on the polarity of the workpiece, a distinction is made between two processes. The choice of system – CDC or ADC – depends on the requirements profile of the component and the area of application.
Cathodic dip coating
In the cathodic dip coating (CDC) process, the workpiece is used as a cathode (negatively charged). The positively charged paint particles migrate to the surface, accumulate and form a resistant film.
Today, cathodic dip coating is the most widely used e-coat process in the world – particularly in automotive engineering, mechanical engineering, the construction industry and wherever maximum corrosion protection is required.
Anodic dip coating
In anodic dip coating (ADC ), the workpiece becomes the anode (positively charged). The negatively charged paint particles migrate to the surface.
ADC is preferably used in areas where decorative properties, high colour stability and a fine surface quality are paramount – for example in the furniture industry, household appliances or consumer goods.
E-coating: properties and advantages at a glance
Uniform layer thickness - even in hard-to-reach areas
A key advantage of e-coating is the even distribution of the paint layer - even on edges, inner surfaces or complex geometries. In contrast to spraying processes, the coating forms wherever an electric current flows. This ensures a continuous, high-quality coating without material build-up or defects.
Excellent corrosion protection - especially for CDC applications
An e-coat achieves excellent corrosion protection values, particularly with cathodic dip coating (CDC). The dense, well-adhering paint film acts as a barrier against moisture, oxygen and aggressive media. This makes the process ideal for applications in the automotive or construction industry, where components are exposed to decades of stress.
High process reliability - standardised, reproducible process
Thanks to automated and precisely controllable process parameters (e.g. voltage, dipping time, bath temperature), e-coat coatings can be produced with high repeat accuracy. This increases quality assurance and reduces rejects. Consistent product quality is a clear competitive advantage, especially in large-scale production.
Environmentally friendly - water-based systems, recovery of excess paint
Modern e-coat systems are based on water-dilutable dispersions and contain only small amounts of organic solvents. Excess coating material is recovered by means of ultrafiltration and fed back into the process. This results in material utilisation of up to98% - a significant contribution to sustainable production.
Economical - high degree of automation, low material losses
The combination of high process stability, minimal waste and material recovery results in low unit costs - even for complex workpieces. The degree of automation enables continuous production with low labour resources. For companies with medium to high production volumes, coating with an e-coat system offers an excellent price-performance ratio.
E-coating process - explained step by step
E-coating takes place in several precisely coordinated steps. The following process description is based on the proven E-coating process from FreiLacke:
1. Pre-treatment
A clean substrate is essential for the quality of the dip coating.
- Degreasing: removal of oil, dust and grease
- Rinsing: complete rinsing of cleaning agents
- (optional) Pickling: removal of oxides from metallic materials
- Phosphating/passivation: Improvement of paint adhesion and corrosion protection
- Rinsing (demineralised): Avoidance of residues
- (optional) Drying: preparation for the dipping process
2. E-coating
The actual e-coat process takes place in an immersion bath with an aqueous dispersion of coating polymers, pigments and additives.
- Immersion: the workpieces are guided into the paint bath
- Power supply: a DC voltage ensures that the paint particles are deposited
- Deposition: a uniform paint film forms on the surface
- Ultrafiltrate rinsing: recovery of excess particles, reduction of rejects
3. Curing/drying
The coating must then be baked by heating to create the desired properties.
- Heating: slow heating of the coated parts
- Cross-linking reaction: formation of a resistant, adhesive film
- Cooling: Preparation for further processing
Visualisation of the process: Continuous system for e-coating
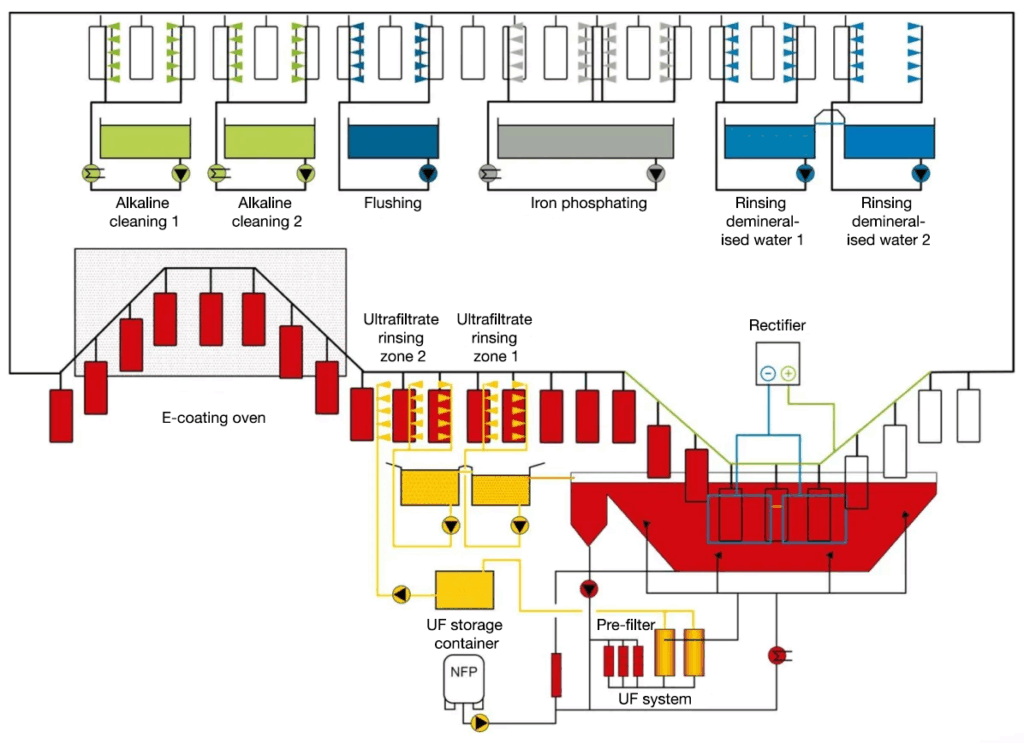
Alkaline cleaning
Removal of oil, grease, dust and other organic contaminants from the workpiece surface. This can be done using alkaline, acidic or neutral cleaners in spraying or immersion processes.
1 of 6Phosphating/passivation
Phosphating: Creates a microcrystalline phosphate layer on the surface, which serves as an ideal adhesion base for the paint and significantly improves corrosion protection.
Passivation: For some metals (e.g. aluminium), a passivation layer is created to increase corrosion resistance and improve paint adhesion.
2 of 6Rinsing
A final rinse with demineralised water removes all remaining chemicals and mineral salts that could impair the quality of the paint film.
3 of 6Immersion
The pre-treated workpieces are immersed in the dip tank. They are electrically conductive and are connected to one of the two poles of a DC voltage source (cathode for cathodic ETL, anode for anodic ETL). The layer thickness is influenced by the applied voltage, the immersion time and the conductivity of the bath.
4 of 6Ultrafiltrate rinsing
After dip coating, the workpieces are usually rinsed with ultrafiltrate from the dip tank. This serves to rinse off excess paint material and return it to the process, which increases efficiency and environmental friendliness to almost 98%.
5 of 6Stoving
The deposited paint film is not yet fully cured and must be cross-linked by heating in order to obtain its final properties. This step takes place in a drying oven.
6 of 6Suitable materials for electrocoating
Electrical conductivity is essential for the application of e-coating. Only then can the coating particles migrate to the surface of the workpiece under the influence of a DC voltage and deposit evenly. Therefore, only metallic substrates that can conduct electricity are suitable.
Materials that are suitable for the e-coat process are primarily
- Steel – widely used in the automotive, mechanical engineering and construction industries
- Galvanised steel – offers additional protection against corrosion
- Aluminium – particularly light, often used in the electronics and furniture industry
- Various cast variants – e.g. cast aluminium
Non-conductive materials such as plastics cannot be coated using this process.
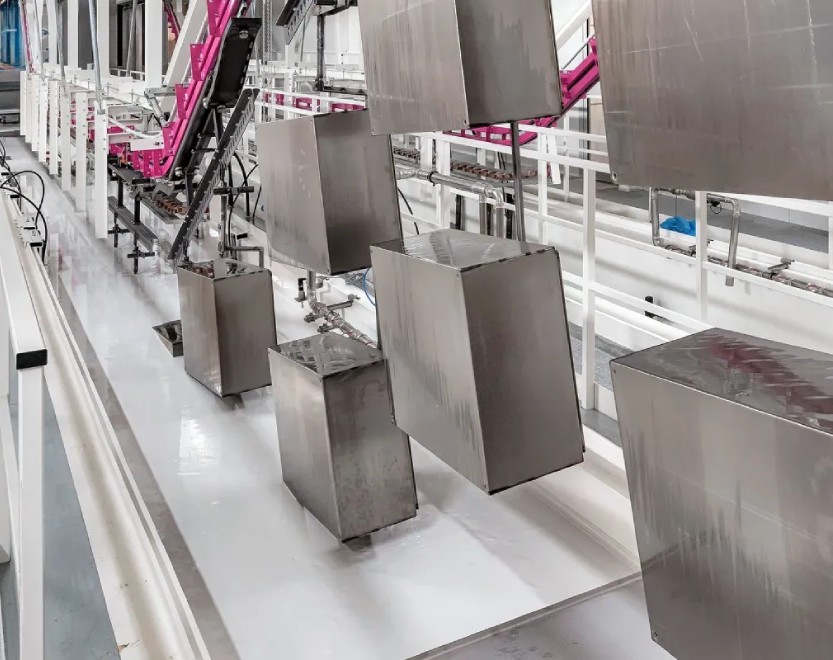
E-Coat in practice
The areas of application for e-coating are diverse. The process is particularly suitable for large quantities or complex geometries where uniform coating distribution, reproducibility and reliable corrosion protection are required.
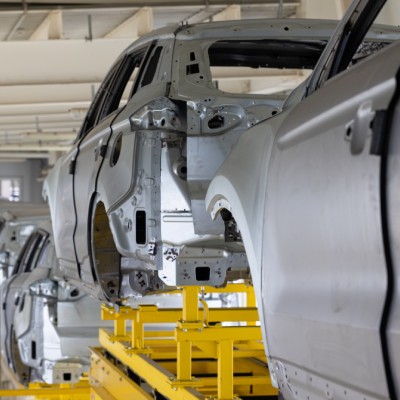
Automotive engineering
The automotive industry uses e-coating in particular to coat body and structural parts. The process makes it possible to evenly coat hard-to-reach interior spaces and hollow profiles – a key aspect of long-term corrosion protection for safety-relevant components. Cathodic dip coating (CDC) is now standard in OEM processes.
Construction industry
Construction elements such as window frames, doors, façade components or railings made of steel and aluminium benefit from durable protection against moisture, road salt and UV radiation thanks to an e-coat. In the construction industry, e-coating is becoming increasingly important as a pre-treatment, as the coating can be easily combined with subsequent powder coating or liquid coating layers.
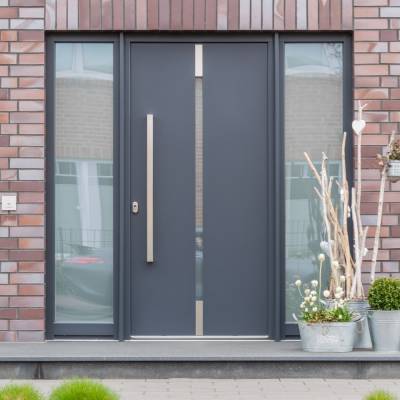
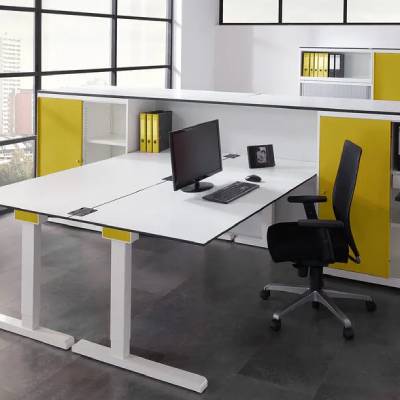
Furniture industry
Metal frames, fittings, connecting elements and structural components in furniture construction are coated efficiently and durably with e-coating. In addition to the protective aspect, the possibility of colour-accurate and decorative further coating also plays a role here.
Enclosures for switch cabinets, heat sinks, connectors and other electronic components are reliably protected against moisture and corrosion with an e-coat. The uniform coating thickness and good edge coverage prevent electrical leakage and ensure a high level of operational safety.
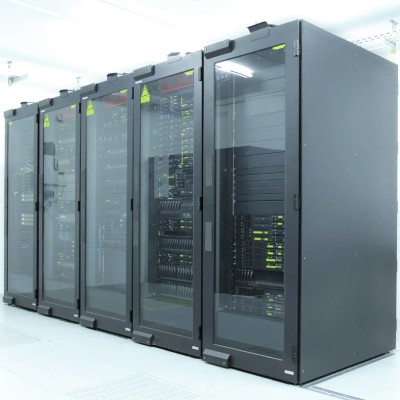
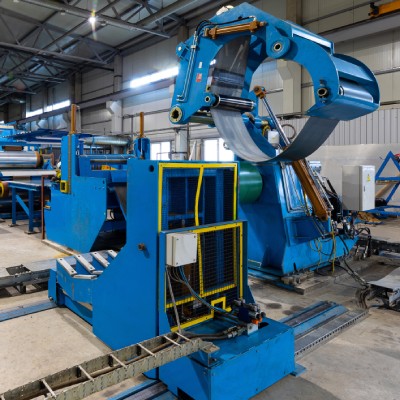
Mechanical engineering
Robust and weather-resistant coatings are essential in mechanical engineering. An e-coat reliably protects frames, housings, brackets and support structures against corrosion, even under extreme operating conditions. Thanks to the high penetration depth, the process is also ideal for complex welded assemblies.
Added value through system coatings - combination with powder and liquid coatings
An e-coat is also ideal as a primer in combination with powder coatings or liquid paints. As part of system coating solutions – one of FreiLacke’s core competences – the electrocoated primer is combined with matching top coats.
These system coatings offer numerous advantages:
- maximised corrosion protection: an e-coat protects as a primer, while the top coat absorbs mechanical and UV stresses.
- Wide range of design options: Powder coatings enable decorative surfaces with textured and gloss effects.
- Process efficiency: Both processes can be easily automated and combined.
- Cross-industry standards: System coatings comply with international standards – ideal for export-orientated manufacturers.
Thanks to its excellent adhesion and chemical compatibility, E-Coat has become an indispensable basis for complex coating systems with high technical requirements.
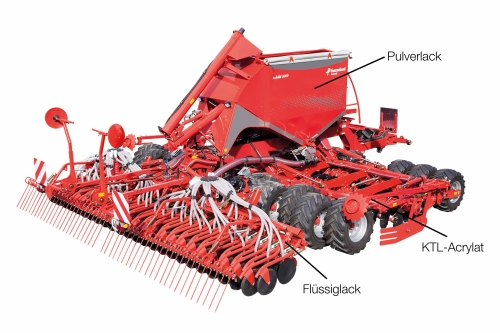
Why e-coats from FreiLacke?
As one of the leading suppliers of electrocoatings, FreiLacke offers proven system solutions – from primers to top coats. With our comprehensive process expertise and high-quality e-coat products, we set standards in the industry.
Your advantages with FreiLacke:
- Customised coating systems for individual requirements
- modern production standards “made in Germany”
- Highest quality and environmental compatibility
- Technical advice from experienced application engineers
Let us provide you with comprehensive advice – our experts are on hand to answer all your questions about dip coating and system coatings.
Unsere Fokusthemen als Lackhersteller